January 1
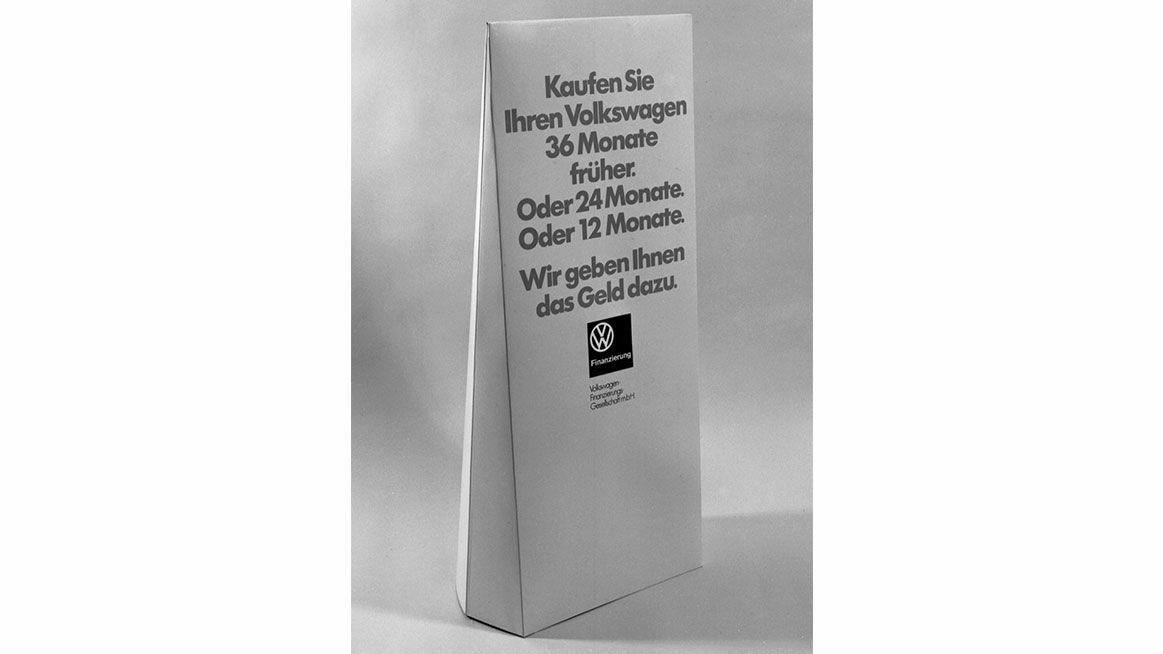
The new generation of Volkswagens arrived at the right time. It helped Volkswagenwerk AG out of the grave situation caused by the oil crisis of 1974/75 and the global recession that acutely threatened the company’s liquidity. The positive response to the Passat and the sales successes of the Golf, which led the German new car registration statistics from 1975 and instigated the compact car class, eased the overall reduced demand for automobiles on the domestic market. While the sales of other manufacturers declined by as much as 40 percent, Volkswagen was able to stabilise its 1975 figures at the previous year’s level. Most of the financial losses resulted from declining exports to Europe and North America. Earnings also declined in South Africa and Mexico, in spite of Volkswagen’s position as market leader, as costs exploded due to inflation and the exchange rate shifts could not be offset by price increases. The decline in sales on the export markets led to overcapacity at the domestic plants, with capacity utilisation dropping to 61 percent in 1975. Aligning production to sales necessitated a substantial reduction of the workforce. After some initial conflict, this was achieved in a socially acceptable manner by mutual agreement between the General Works Council and the company management. In 1976, Volkswagenwerk AG increased sales by more than 15 percent; the Volkswagen Group had overcome the crisis.
The launch of four new model series within just a few years was accompanied by far-reaching changes in production. In order to apply the traditionally high level of production mechanisation to the multi-model range, innovative technical and organisational production systems were required. To that end, between 1972 and 1975 the company launched a DM 2.5 billion investment programme which established the production engineering basis for the new product range. In 1973 Volkswagen converted the plants in Wolfsburg and Emden to hanging assembly line systems, thereby improving production flexibility and enhancing assembly conditions. Rationalisation was substantially enhanced by computer systems, for example in the press shop, where production was now controlled and monitored centrally. The company limited the production of air-cooled engines, while increasing capacities for water-cooled engines and introducing corresponding new manual and automatic transmissions into its range. Volkswagenwerk AG gradually established the preconditions to implement its modular component kit system, allowing use of the same parts in different models with largely identical technical specifications. The Passat was closely based on the Audi 80, while the Polo originated from the identical design of the Audi 50. The modular component kit system was an essential element of the new production concept aimed at safeguarding the company’s long-term profitability.
After the first phase of rationalisation was completed, Volkswagen concentrated on increasing its exports, especially to the USA, where the downward trend continued. Between 1973 and 1976, Volkswagen of America’s sales dropped from 540,364 to 238,167 vehicles; its market share was cut in half to 2.3 percent. The Volkswagen management had already started thinking about setting up a production facility in America back in 1973, in order to compensate for competitive disadvantages in pricing resulting from unfavourable exchange rates and West Germany’s high production costs. The main objection to this project was the tie-in to one model, and the resultant high degree of product dependency in a competitive market, whereas the alternative idea of upgrading production in Mexico to supply the USA raised concerns with regard to product image. But falling sales and financial losses from the export business finally brought acceptance of the idea that the only way to uphold the company’s key export bastion was to produce locally. Moreover, the strong initial success of the Golf also prompted the decision in June 1976 to build the Rabbit, the American version of the Golf, in the USA. The plant in Westmoreland began producing for the North American market in April 1978, after Volkswagen of America had the previous year succeeded in reversing its trend by achieving a 22 percent sales increase. Initially, not even the global recession beginning in 1980 or the massive competition from Japanese manufacturers, who dramatically cut the global market share of US car-makers within the space of a decade, had a negative impact on sales. Following a 13 percent rise in 1979, the US subsidiary reported a further rise in sales from around 337,000 to 368,000 Volkswagen and Audi models the following year. The company was benefitting in this from the dramatic rise in oil prices, which triggered growing demand for vehicles offering better fuel economy.
In order to stabilise its position in South America, Volkswagen took over the faltering Chrysler Corporation’s Brazilian subsidiary in 1979, and in 1980 acquired its Argentinian subsidiary too. The restructuring of Chrysler Motors do Brasil Ltda. as a dedicated truck-maker additionally strengthened the international supply network in the commercial vehicles sector. Volkswagen thereby intensified its involvement in the sector that had been instigated in 1977 by its co-operation agreement with Maschinenfabrik Augsburg-Nürnberg AG (M.A.N.). Volkswagen gradually expanded its commercial vehicles product range from 1975 onwards, creating a diversity of models similar to that in its car business. Along with the classic Transporter, the range included the LT, a light truck series developed jointly with M.A.N., as well as the truck built in Brazil starting in March 1981. The start of production of 11- and 13-tonne trucks by Volkswagen Caminhões Ltda. coincided with a dramatic downturn in the South American economy. Annual inflation rates of well over 100 percent as well as restrictive monetary and import policies led to a collapse in passenger car sales in Brazil and Argentina in 1981. Volkswagen do Brasil’s unit sales were 35 percent down against the previous year. Sales of Volkswagen Argentina S.A., which at the end of the year switched to assembling the Transporter from Brazilian component kits, fell by a third. At Volkswagen of America, too, 1981 saw a reversal of the sales trend. The following year there was a 40 percent slump in sales, due in part to the global economic crisis and in part to Japanese competition. The second assembly plant in Sterling Heights completed in 1982 did not go into operation and was sold in 1983.
Domestic demand was impacted by the second oil crisis, especially in the compact executive (D segment) class. While Audi suffered a drop in sales in 1980, Volkswagen profited from the shift to more economical models. The Golf, Golf Diesel and new Passat were successful in a declining market, enabling the Volkswagen Group to hold on to its market share of just under 30 percent. A greater cause for concern even than the unstable energy situation was the expansionist strategy of Japanese manufacturers, who by now were making more than one in five cars worldwide, and were gaining market shares in both America and Europe. Their success was based on a flexible, horizontal manufacturing system which enabled them to produce low-priced models and adapt quickly to changing customer needs. Up to then Volkswagen had strongly defended its position in the face of far-eastern competition, as its higher retail prices were backed by high standards of engineering and product quality, a superior sales and service network and the high resale values of its models. However, the shift in the Japanese exporters’ focus from the USA to Europe in 1980 resulted in a competitive battle that could not be won on the price front alone. The Volkswagen Group’s strategy was to concentrate on maintaining its technical edge and increasing the flexibility of its manufacturing system in order to adapt its production volumes, models and equipment specifications to the increasingly diverse demand.
Between 1979 and 1982, Volkswagenwerk AG invested around DM 10 billion in its German operations, primarily in the ongoing development of energy-saving, eco-friendly models and in rationalising production. The automation phase was marked by the introduction of micro-electronically controlled industrial robots, multi-purpose machinery capable of handling different vehicle types and models, and variable conveying systems. With the help of new control systems in the body shop, paint shop and final assembly, each vehicle could be handled as a custom order, and built according to individual customers’ preferences. Computer-controlled material flow and high-shelf storage with driverless transport systems improved the efficiency of materials management. In 1981, the type-specific mechanised operation of the body shop was converted to programmable handling machines. The high-point of these modernisation measures was the first ever fully automated car assembly line, which was commissioned into operation in shed 54 at the Wolfsburg plant.
Thus strengthened to meet the intensified competition, the Volkswagen Group set out on an expansionist course. Because of the limited growth possibilities on the domestic market, long-term survival depended on exploiting opportunities for expansion on international markets. The boom in the car industry over the coming decade provided favourable conditions for that undertaking.