January 19
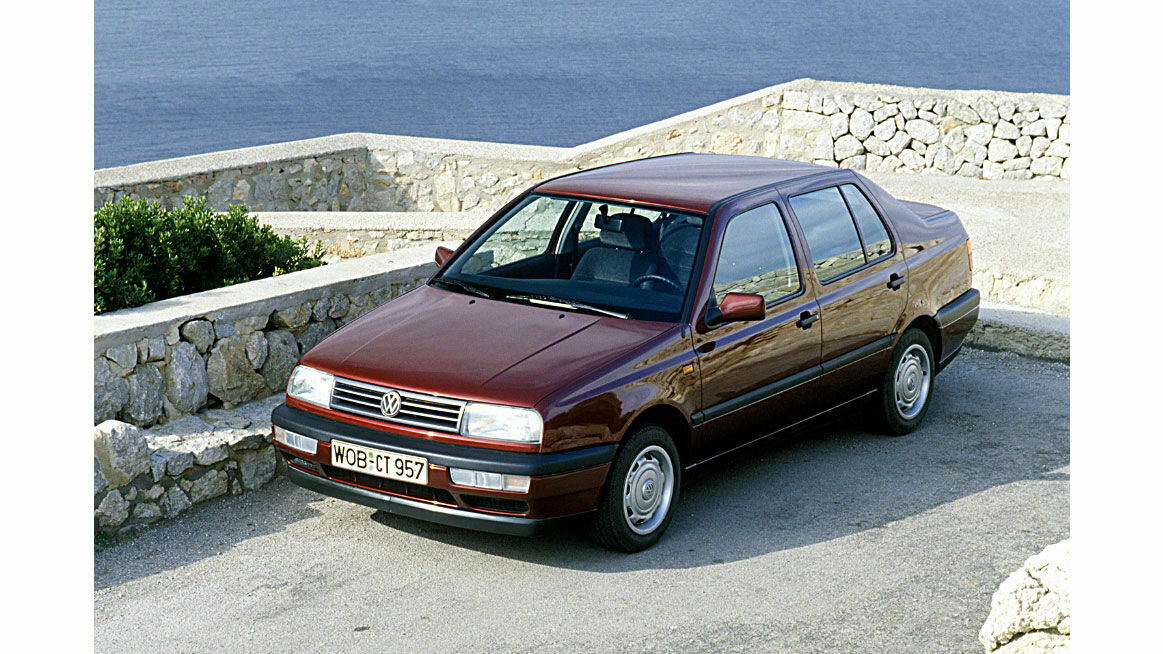
The Volkswagen Group initiated a strategic change of direction during the severe global recession of 1992/93. While the 1980s was a time of internationalisation and volume policy, Volkswagen now concentrated more on product diversity as well as on improving productivity and earning power. The Group’s modernisation was linked to a globalisation process aimed at establishing highly efficient production facilities and effectively reshaping the functional division of labour within the global production alliance. The Wolfsburg-based car-maker was responding to structural problems specific to the industry and the company itself which became more pronounced during the recession as sales plummeted. Price competition, particularly from Japan and the emerging Korean automotive industry, increased the pressure on the global player to streamline and cut costs, while market saturation in Western Europe dampened growth expectations as the economic upturn triggered by German reunification petered out.
To manage the crisis, the Volkswagen Group began to reorganise its production system along the lines of lean production characterised by flat hierarchies, team working, less manufacturing depth and logistical networking with suppliers. Proactive support from the Works Councils was vital to the success of this medium-term project. The same was true with regard to the transition to a socially sustainable, market-oriented employment policy, based on rapid adaptation to customers’ wishes and fluctuations in demand rather than merely on steady utilisation of capacity. This difficult synthesis was achieved for a time by the four-day week introduced with effect from January 1, 1994. The flexible model based on cutting weekly working time at Volkswagen Aktiengesellschaft from 36 to 28.8 hours a week was an innovative instrument aimed at reducing the excess manpower resources estimated as 30,000 posts. At the same time, Volkswagen moved ahead with the introduction of lean production and globalisation in order to bring about a sustained improvement in cost structures.
The factories built in the early 1990s were models of lean production. The Mosel plant in eastern Germany and the Seat plant at Martorell were organised along the lines of Japanese transplants. Production processes at the existing plants were systematically improved, mainly as new models were launched. The platform strategy made a substantial contribution to establishing efficient plant structures. By interlinking the Group’s 16 platforms, and gradually reducing their number, Volkswagen cut back development and manufacturing depth while simultaneously raising product quality and offering customers a more differentiated product range. The platform strategy went hand in hand with a new procurement policy named Global Sourcing. The object of procuring from all over the world was to establish long-term networking between development, production and logistics operations on the one hand and low-cost, high-performing system suppliers on the other for the “just in time” supply of complex components and modules. The Volkswagen Argentina plant opened in 1995, for example, operates on the modular assembly principle, whereby suppliers autonomously install their pre-assembled components on-site. In the 1990s, Volkswagen resorted more extensively to external suppliers for production in Germany too, putting pressure on the Group’s in-house suppliers to cut costs and establish systems expertise.
The introduction of decentralised production management anchored the principle of lean production in work organisation. Volkswagen began pushing ahead with the introduction of team working accompanied by flatter hierarchies in 1992. In 1993, the elimination of entire management levels shifted decision-making competencies to the operating units, so promoting independent responsibility and enhancing employee motivation. In parallel, Volkswagen implemented the continuous improvement process perfected by the Japanese. Employees were encouraged to participate in optimising their own workplace to raise the quality and productivity of all production processes. The transition in 1993 from sequential vehicle development to Simultaneous Engineering, which shortened project lead times and facilitated a faster, more customer-oriented response to market changes, pursued the same goal.
The restructured production system began to achieve measurable success after a few years. Between 1994 and 1996, productivity in the Volkswagen Group rose by almost 30 percent, while production costs fell as a result of shorter production times. By 1997, the core production time for the Polo had gone down from 24 hours to 15, and for the Passat from 31 to 22. The advantages of lean production became clear to all in the fourth generation of the Golf, which went into production at four plants in 1997. It impressed with high quality standards and environmentally friendly technology. Volkswagen Aktiengesellschaft systematically enhanced its in-production and product-integrated environmental protection over the following years based on the advancement of direct fuel injection and light-weight construction techniques and the creation of a product life-cycle management system.
Growth driven by new products, increasing both sales and earnings, lent impetus to the expansion of the multi-brand strategy. In 1998, Volkswagen brought the legendary Bentley, Lamborghini and Bugatti brands into the Group with a view to expanding the product offering in the luxury segment. The Volkswagen brand added its own luxury saloon, the Phaeton, to that segment offering in late 2001, and successfully moved into two new market segments the following year with the launch of the Touareg luxury SUV and the Touran compact MPV. At the organisational level, restructuring of the business lines was flanked by ongoing efforts to cut costs by increasing flexibility and standardising the complex production structure of the Volkswagen Group.
Ferdinand Piëch, appointed Chairman of the Board of Management in 1993, strengthened the international competitiveness of the Volkswagen Group by setting up a flexible global production network. Under his leadership, globalisation of the Group progressed further. Various models destined for the world market were produced exclusively at international sites: the New Beetle and the Jetta in Mexico, the Touareg in Slovakia, the Sharan in Portugal, the Caddy in Poland and the Fox in Brazil. Piëch’s successor Bernd Pischetsrieder continued to develop Volkswagen as a powerful multi-brand group from 2002 onwards. The priority task was to cut costs along the value chain, and a performance enhancement programme was therefore launched in 2004. The 2004 and 2006 collective agreements between the unions and management of Volkswagen Aktiengesellschaft marked further steps towards improving earning power.
In 2007, new Chairman of the Board of Management Martin Winterkorn formulated an unambiguous growth strategy, with the aim of making the Volkswagen Group the biggest-selling and most sustainable car-maker and turning Volkswagen into the world’s most innovative volume brand by 2018. In order to achieve those ambitious goals, the multi-brand Group intends to win new customers with intelligent product innovations and harness the expansion potential offered by emerging markets. By building production plants in Russia and India, the Volkswagen Group has established a very promising competitive position to exploit the enormous growth potential of those emerging automotive markets. In the People’s Republic of China, Volkswagen faces the challenge of maintaining the leading market position it has enjoyed almost uninterruptedly since 1985 in the face of competition from US and Japanese car-makers, who significantly expanded their manufacturing capacity once China joined the World Trade Organization in 2004. Despite intensified competition, China has become by far the largest single market for the Volkswagen Passenger Cars brand. By 2012, Group sales had soared to 2.815 million vehicles.
With its record sales and earnings achieved once again in 2012, the Volkswagen Group is well placed to combine volume growth with a rise in productivity. To make sure the company continues on the right track, Volkswagen is intent on optimising workflows and process organisation. Furthermore, the growing number of cross-brand vehicle modules will help to cut development and production costs and accelerate product innovations. The increased complexity demands new solutions for long-term management of processes. The Volkswagen Group is also fulfilling its responsibility to humanity and the environment in pursuit of its goal of being recognised as the world’s most sustainable car-maker. The need to generate profits while consistently innovating and acting in keeping with corporate social responsibility underscores the challenge which the robust, multi-brand Group is mastering.